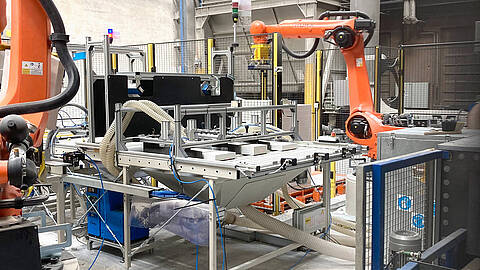
Robot cell for new customer PORFIX
Precise prototype
Aerated concrete is light but stable, resilient but non-combustible and provides good thermal insulation. No wonder that shaped blocks made of aerated concrete are very popular in house construction. PORFIX - pórobetón, a.s. is the leading manufacturer in Slovakia of plane and partition blocks, lintels and U-profiles made of this mineral building material. A robot cell has recently been installed in the production hall in Zemianske Kostolany, in the heart of Slovakia: Blumenbecker Slovakia s.r.o. developed a prototype for bonding U-profiles in close cooperation with Porfix.
Automation in production - more efficiency, less waste
This project is also the first collaboration between the two companies. When the order came for the development of the prototype, the real work began: ‘This is not a standard application and is completely new territory for us,’ explains Peter Grňo, Managing Director of Blumenbecker Slovakia.
The new production method is fundamentally different from the traditional variant. Previously, the U-profile was milled from a block of aerated concrete. On the one hand, this resulted in a lot of waste. On the other hand, broken edges were created. In addition, the work process was a dusty affair. Now the U-profile is no longer made from one piece, but from three.
How a U-profile is created
There are two Kuka robots in the robot cell. Robot 1 picks up the centre piece from the stack and places it on the gluing station. The adhesive is applied there. It then picks up the centre piece again and places it on the conveyor belt. Robot two, meanwhile, picks up the two side pieces and places them on the conveyor belt as well. A machine glues the three parts together as a U-profile and the adhesive dries. Finally, robot 2 picks up the finished U-profile and places it on a pallet.
‘The advantage is that you get a very cleanly worked end product. You can saw the centre piece to different widths and get different sizes,’ Grňo explains.
‘This automated line will increase production efficiency and significantly reduce the amount of waste generated by the previous production method by milling.’
Erik Hojč, Produktionsleiter, PORFIX – pórobetón, a.s.
Compressed air and the right adhesive
One challenge was the selection of the perfect adhesive. Many tests were carried out together with the customer. ‘Not only the hold was important. The drying time also had to be integrated into the work process,’ Grňo knows.
The Blumenbecker engineers came up with something special to transport the three sections: The robots were given a compressed air attachment. This allows the parts to be sucked in. However, the air flow can also be reversed.
When the pieces are sawn into the right sizes, a lot of dust is produced that still sticks to the pieces. The compressed air attachment blows the dust away beforehand. Only then is the respective piece picked up. It is free of sawdust and thus perfectly prepared for the work process.
And what does the customer say? Erik Hojč, Production Manager at PORFIX - pórobetón, a.s. is delighted: ‘I would like to thank Blumenbecker and my production colleagues who developed this prototype together.
This automated line will increase production efficiency and significantly reduce the amount of waste generated by the previous production method by milling. Thank you very much! We will be happy to try it out elsewhere in production.’