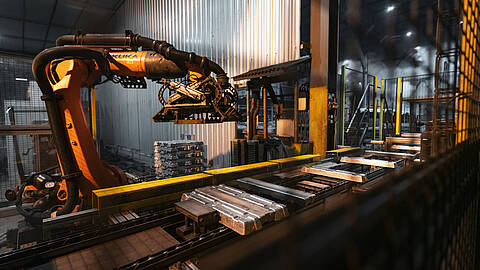
Robotická paletizace hliníkových ingotů
Náš zákazník: Saker spol. s.r.o. – o.z. Alusak
Společnost Alusak byla založena v roce 2006 jako odštěpný závod skupiny Saker a zaměřuje se na zpracování hliníkových odpadů a výrobu hliníkových slitin. V roce 2008 provedla zásadní inovaci nahrazením kelímkových pecí technologií tavení v rotačních pecích, což vedlo k zvýšení výrobní kapacity a zlepšení kvality slitin. Společnost dále rozvíjela tuto technologii a investovala do moderních systémů hoření a filtrací, aby zajišťovala ekologickou čistotu provozu.
Paletizace ingotů z hliníkového odpadu
Automatizovaný proces paletizace ingotů představuje inovativní řešení pro zvýšení efektivity v průmyslové výrobě. Společnost Saker s.r.o., o.z. Alusak, implementovala tuto moderní technologii s cílem minimalizovat ruční práci, maximalizovat produktivitu a zajistit konzistentní kvalitu výstupních produktů. Projekt zahrnuje komplexní systém od odběru ingotů z licího pásu až po finální balení.
Popis projektu
Celé pracoviště, s robotem KUKA, je umístěno na konci stávajícího dopravníku. Odlitky vyklopené z forem licího pásu postupně dojedou na řetězovém dopravníku, přes chladící vodní zónu, až na začátek vstupního dopravníku robotické linky. Jednotlivé odlitky mají v průběhu licího procesu částečně proměnnou vlastní velikost a hmotnost.
Vstupní dopravník celého pracoviště je osazen prvky, které vyhodnocují v reálném čase velikost každého ingotu. Ingoty, které neodpovídají nastavenému rozmezí, jsou označeny jako NOK, a odjíždějí z linky samostatným výstupem. Z důvodu lichoběžníkového tvaru ingotů, je každý druhý (pro každou skládanou vrstvu) před svým příjezdem k místu odběru robotem otočen tak, aby pětice ingotů vždy vytvořila ucelenou plochu. Vrstvy ingotů robot ukládá vzájemně křížem na sebe za účelem dostatečné stability. Počet vrstev zadává obsluha pracoviště do programu robota předem. Každá naskládaná paleta je automaticky vážena a potištěna interními informacemi z nadřazeného systému.
V případě poruchy robota je plynulý chod výroby zajištěn přidáním zásobníku pro ruční skládání na konec dopravníku, bez nutnosti zastavení výroby.
Řídící systém linky je spojen komunikační sběrnicí s nadřazeným systémem pro efektivní řízení výroby a její sledování v reálném čase. Automatické ukládání dat linky na straně řídícího systému PLC, v případě výpadku komunikace, zajišťuje jejich bezpečnost i při nestandardních událostech. Výstupní dopravník má několik funkcí. Slouží k vyvezení hotových vrstev za výstupní vrata linky, jako buffer hotové výroby a také jako místo páskování. Celý prostor výstupního dopravníku je, pro jeho různá využití, optimalizován nejen pro automatický režim, ale také pro snadný a bezpečný přístup obsluhy.
Naše technické řešení splnilo požadavky zákazníka na zvýšení produktivity výroby, odstranění velmi namáhavé ruční práce, minimalizaci ztrát způsobenou chybnou manipulací a zajištění trvalé kvality výstupního produktu.
Our customer says:
» Od samého začátku jsme byli spokojeni s profesionálním přístupem společnosti BPR.
A ač řešení nebylo vzhledem k našemu provozu jednoduché, vše se zprovoznilo na první pokus a v termínu. «