
Modernization of a fiber cement processing plant Industrial assembly for Etex Germany Exteriors GmbH
The air is warm. So warm that sweat is running from under your helmet. It smells of damp cement, wood and a bit like chemistry lessons in year 10. You can literally taste the dust on your tongue. And it's loud. It's a hive of activity here - rolling, pressing, drying and stacking. The mixture is prepared in huge wooden vats, a pale, pulpy mass. It's hard to believe what will come out of this later.
Behind the centrepiece - the fibre processing plant - there are two gigantic machines in the hall that produce quality fibre cement products from the contents of the wooden chests. The fibre processing plant dates back to the 1960s. It was time for a modernisation in which Blumenbecker was able to demonstrate its expertise in industrial assembly.
The Etex Group is a leading manufacturer of building materials and is active in over 40 countries worldwide. At its production facility in Neubeckum, Etex Germany manufactures fibre cement products, including roof panels. One of the most popular products is called ‘Natura’. You can still see the fibres in these anthracite-grey façade panels. This exterior cladding can be found on several schools in the neighbourhood. The company attaches great importance to safety in production and sustainability. At the end of 2021, the largest photovoltaic system in the district until recently was put into operation on building 3 of the factory premises.
Complex task
The tendering phase was a good two years ago. After several negotiations, consultations and discussions, Etex commissioned Blumenbecker 2023 with the industrial assembly and delivery of the switchgear for the modernisation of the pulp preparation plant. ‘Complexity, adherence to deadlines and conversion during ongoing operation were the biggest challenges in the project,’ summarises Maxim Unrau, Technical Engineering/Exteriors at Etex in Neubeckum, adding: ’The documentation for our plant from the 1960s was outdated and not quite complete. We were able to rely on Blumenbecker's professionalism, expertise and excellent cooperation.’The old control room no longer offered enough space and was in need of renovation.
A new one was built. Meanwhile, Blumenbecker Automatisierungstechnik GmbH in Beckum built the modern switchgear, which is designed for an output of up to 4,900 amps and consists of four main cabinets, six floor cabinets and various field devices such as level and radar sensors. The enclosures in production are made of stainless steel to withstand the warm, humid ambient air. Etex came to the Blumenbecker production hall for the acceptance test. ‘The local connection is another plus point. The switchgear met our expectations and we are very satisfied with the result,’ confirms Unrau.
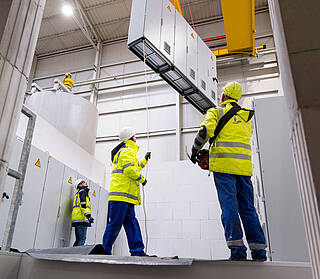
Conversion during ongoing operation
From November 2023, the installation team at Etex was busy dismantling the system, laying new cable routes and making preparations for the installation. ‘Carrying out this work during ongoing operations requires good coordination between everyone involved. We are very satisfied with the experienced installation management and the team. They responded flexibly to change requests and provided constructive suggestions, which were also incorporated,’ explains Unrau.
The switchgear was delivered at the end of March 2024. The new brick switchgear room in the raw materials hall has a double floor for the cables. What it didn't have at that time, however, was a roof. And for good reason: due to the size of the switch cabinets, it was not possible to push them through the door. This was already clear at the planning stage. So the switch cabinets had to be lifted into the room using the overhead crane. Millimetre work that worked.
»Complexity, adherence to deadlines and conversion during ongoing operation were the biggest challenge in the project.«
Maxim Unrau, Technical Engineering/Exteriors,
Etex Germany Exteriors GmbH
The next task for the installation team was to lay cables, and not in short supply. The fitters pulled and laid twelve kilometres (!) of cable. Or to put it in terms of weight: eight tonnes of heavy work for the men. ‘A weighty project that our industrial assembly team mastered during ongoing operations,’ reports Markus Windhövel, Team Manager Industrial Assembly & Services at Blumenbecker.

Reliable partner
The new switchgear was commissioned during the summer holidays. Production was then shut down for six weeks. ‘There has never been such a long shutdown in our company history in Neubeckum. This requires precise planning in-house and a partner we can rely on. And we have that with Blumenbecker,’ says Unrau. However, the project is not yet complete after commissioning. The installation team is then deployed again - to dismantle the old cabling and remove the old control room. Then the air is still warm. So warm, in fact, that sweat runs down from under the helmet.
Current issue as flip book
In this issue, you will find a wide range of customized solutions for our customers, whether in rail technology, industrial assembly or industrial services for passenger bridges in the shipping industry. Enjoy reading and discovering.
Flip book