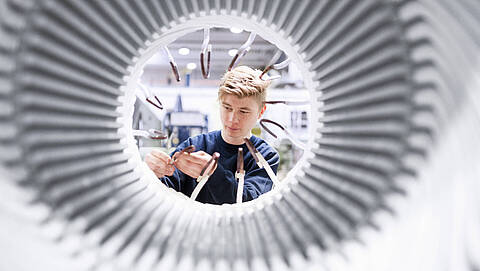
Wartung, Prüfung und Reparatur von elektrischen Maschinen
Umfassender Service für elektrische Maschinen
Unser Industrieservice bietet Ihnen herstellerunabhängige Wartung, Prüfung und Reparatur von elektrischen Maschinen wie Elektromotoren und Generatoren. Unsere Experten sind spezialisiert auf die Instandhaltung und Neuwicklung von Elektromotoren aller Fabrikate sowie Generatoren, Pumpen, Schweißmaschinen, Elektromagneten und Antriebsmaschinen. Unser Ziel ist es, Ihre Maschinen in einem Zustand zurückzuliefern, der dem Neuzustand möglichst nahekommt.
Wir führen regelmäßige Wartungs- und Instandhaltungsarbeiten an allen elektrischen Maschinen durch. Zu unseren Kunden zählen renommierte Unternehmen wie Westfleisch, Kaldewei und Rottendorf Pharma.
Unsere moderne Reparaturwerkstatt ist mit Ausschwelofen, Vakuumtränkanlage, computergesteuerter Wuchtbank, neuestem Prüffeld und Krananlagen bis 25 Tonnen ausgestattet. Die Neuwicklung von Läufern und Ständern gehört zu unseren täglichen Aufgaben. Wir setzen ausschließlich modernste Messgeräte und Verfahren ein und liefern Ihnen eine lückenlose Dokumentation aller durchgeführten Arbeiten.
Wir verfügen über ein umfangreiches Lager an Ersatzteilen für Elektromotoren zahlreicher Hersteller und bieten Ihnen auf Wunsch auch Neumotoren an. Selbst wenn Ersatzteile nicht mehr erhältlich sind, können wir diese oft selbst herstellen und so die Lebensdauer Ihrer Maschinen erheblich verlängern.
Unsere Schwerpunkte:
- Wartung und Reparatur von Drehstrommotoren
- Instandhaltung von Hochspannungsmotoren
- Reparatur von Gleichstrommaschinen
- Frequenzumrichter Service
- Wartung und Prüfung von Generatoren
- Instandhaltung von Transformatoren
- Service für Notstromaggregate
- Reparatur von Pumpen und Geräten
Explosionsgeschützte Motoren (Ex-Motoren)
In explosionsgefährdeten Bereichen sind sichere und zuverlässige Motoren unerlässlich. Blumenbecker bietet umfassende Wartung und Reparatur von explosionsgeschützten Motoren (Ex-Motoren) gemäß den ATEX-Richtlinien. Unsere speziell ausgebildeten Fachkräfte sorgen dafür, dass Ihre Ex-Motoren stets den höchsten Sicherheitsstandards entsprechen und zuverlässig arbeiten.
Moderne Instandhaltungs Methoden
Laseroptisches Ausrichten
Mit der laseroptischen Ausrichtmesstechnik steigt die Chance, das Ausrichtproblem in den Griff zu bekommen. Als direkte Folge der so verbesserten Ausrichtungen erhöhen sich Wirkungsgrad, Zuverlässigkeit und Lebensdauer rotierender Maschinen. Studien beweisen zudem: Wenn die Ausrichtung um nur wenige 1/100 mm verbessert wird, was mit einem Laserausrichtsystem auf einfachste Art und Weise zu schaffen ist, können mindestens 0,5 Prozent der Energiekosten eingespart werden.
Laseroptisches Maschinenausrichten
Schnelles und genaues Maschinenausrichten mit dem Laser ersetzt die traditionelle und etablierte Methode mit Lineal und Messuhr. Statt nur die Lage der Maschinen- und Kupplungsgeometrie zu bestimmen, werden mit dem Laser die Drehachsen vermessen.
Wie funktioniert die laseroptische Messung?
Laseroptische Messgeräte bestimmen den Grad der Fehlausrichtung, indem sie den Versatz der Wellen messen. Die Laser-/Detektoreinheit (Aufnehmer) und der Reflektor sind mit stufenlos verstellbaren Spannvorrichtungen jeweils auf einer Seite der Kupplung befestigt. Der Laserstrahl des Senders fällt über die Kupplung in ein Glasprisma im Reflektor, wird dort zurückgespiegelt und trifft im Aufnehmer auf einen Positionsdetektor.
Unsere Leistungen im Detail
- Erfassung des Maschinenzustandes
- Messung von Kupplungsversatz, Kupplungsklaffung und Schieflage der Maschine.
- Bildschirmgeführte Korrektur an jedem einzelnen Maschinenfuß.
- Auswertung der aufgenommenen Daten
- Beratung des Kunden und gemeinsame Festlegung der Maßnahmen
- Durchführung der Maßnahme unter Berücksichtigung der kundenspezifischen Terminsituation
Condition Monitoring
- Sicherheit: Basierend auf den in Echtzeit analysierten Sensordaten kann ein verlässliches und sehr schnell reagierendes Sicherheitssystem (Notabschaltung) realisiert werden. Im Vergleich dazu sind bisherige Systeme (z. B. Schwingungssensoren) in aller Regel unpräziser und sie liefern anschließend keinen Beitrag zur Aufklärung des Schadensfalls. Online Condition Monitoring ermöglicht eine Notabschaltung aufgrund der erfassten Daten - und somit eine Analyse über den Störfaktor.
- Maschineneffizienz: Die Überwachung des Maschinenzustands ist die zwingende Voraussetzung für eine "Zustandsorientierte Instandhaltung". Diese Strategie löst die bisher übliche "präventive" Instandhaltung ab. Bei der Letztgenannten wurden in festen Zeitabständen die betreffende Maschine heruntergefahren und Bauteile überprüft bzw. ausgetauscht. Diese Art der Maschinenwartung führte häufig dazu, dass intakte Bauteile ausgetauscht und vorhandene "Restlaufzeiten" somit verschenkt wurden.
Dieses Konzept stellt höchste Anforderungen an Sensorik, Messdatenverarbeitung und anlagenspezifische Kenntnisse. Es bietet jedoch auch das größte Potenzial zur Kosteneinsparung, da die Lebensdauer kritischer Maschinenelemente praktisch vollständig ausgenutzt werden kann und gleichzeitig nötige Instandsetzungsmaßnahmen in Abstimmung mit dem Produktionsplan terminiert werden können.
Die zustandsorientierte Instandhaltung als Querschnittsfach aus den Gebieten Mechanik, Akustik, Systemtheorie, Elektronik und Informatik ist kein fertig erforschter Wissenschaftszweig, sondern befindet sich in einer raschen Entwicklung. Insbesondere bei der Überwachung einzelner Komponenten kann sie jedoch bereits heute sehr treffsicher sein. Bei komplexen Anlagen wird sie aber zunehmend unschärfer, da sich mit steigender Anlagenkomplexität einer immer größere Anzahl von Signalen verschiedenster Herkunft überlagert. Ein weiteres Manko war bisher auch oft das Fehlen geeigneter Sensoren, um Signale direkt in den Verschleiß- bzw. Schädigungszonen aufnehmen zu können. Hier vermag in Zukunft vielleicht die Mikrosystemtechnik Abhilfe zu schaffen, z. B. durch Sensoren in Dünnschichttechnik, die direkt auf der zu überwachenden Struktur angebracht werden können.
Die Herausforderungen dieser Strategie sind zu sehen in
- der Suche nach geeigneten Messstellen und Sensoren,
- dem Finden aussagekräftiger Parameter (Zustandsgrößen) für die Schädigung der interessierenden Komponenten,
- der gezielten Anwendung von Signalanalyse und Mustererkennung
- sowie der enormen Datenflut.
Oder um es in einem Satz zusammenzufassen: Was muss wann wo, wie und womit überwacht werden?
Was Condition Monitoring nicht kann, ist das Erkennen und Vermeiden von spontanen Ausfällen wie z. B. Ermüdungsbruch einer Welle.
Für weitere Fragen stehen wir Ihnen gern zur Verfügung. Nehmen Sie mit unseren Fachleuten für die zustandsorientierte Instandhaltung Kontakt auf.
Schwingungsanalyse
Hier hilft die Methode der indirekten Schadenserkennung durch zyklische Messung der Maschinenschwingungen mit anschließender computerunterstützter Auswertung - die sogenannte Schwingungsanalyse. Die konkrete Ausführung solcher Messsysteme besteht aus fest installierten Messstellen, einem tragbaren Messaufnehmer sowie einem PC mit spezieller Software. Durch die Schwingungsanalyse werden Unwuchten, Maschinenversätze und Lagerschäden vor dem Schadensfall erkannt. Die Trendüberwachung erfolgt durch die Analyse hochfrequenter Lagerschwingungen nach der Stoßimpulsmethode. Die Ergebnisse geben Hinweise auf die Entwicklung der charakteristischen Zustandskenngrößen der Maschinenlager.
Durch die regelmäßige Aufzeichnung dieser Kenngrößen lässt sich ein beginnender Lagerschaden rechtzeitig erkennen und der Lagerzustand zuverlässig beurteilen. So kann man beispielsweise feststellen, ob ein Lager ausreichend geschmiert ist oder trocken läuft. Diese Vorteile und eine einfache Handhabung haben die Stoßimpulsmethode zu einem weit verbreiteten Messverfahren in der Instandhaltung gemacht. Gezielte vorbeugende Maßnahmen wie Ausrichten, Auswuchten und Lagerwechsel machen ungeplante und unwirtschaftliche "Erste-Hilfe-Maßnahmen" überflüssig.