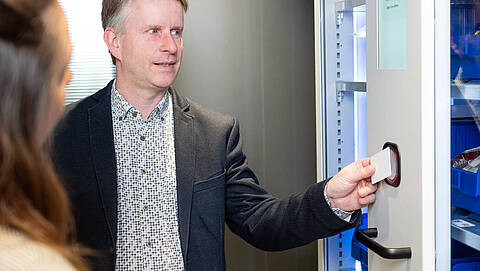
Dispensing machines for C-parts Anything but standard
‘All-rounder’ vending machine
When we hear the word vending machine, most of us probably think of a sandwich for our breakfast break, coffee for a quick caffeine kick or our favourite snack for in-between meals. In addition to food and many other things, there are also vending machines that can do much more than just dispense. Vending machines are intelligent storage systems. One of these ‘all-rounders’ has recently been installed at ekka Entlackung Ernst Kuper GmbH in Iserlohn.
Customer: ekka Entlackung
The company ekka specialises in professional paint stripping and cleaning of metals and other materials. With around 60 employees, the company specialises in high-quality and environmentally friendly paint stripping. In production, work is carried out in three shifts using various processes - seven days a week. The thermal process generates temperatures of up to 450 degrees. The chemical spraying or dipping process is an aqueous-alkaline-based method. Employees in the ‘chemistry’ department need different work gloves to their colleagues in the ‘thermal’ department.
PPE at the touch of a button
In the past, gloves, rubber aprons, dust masks - in short, most of the PPE (personal protective equipment) required - as well as route cards, pens, adhesive tape, etc. were distributed by the respective supervisor. There was a tally sheet for documentation purposes. If a glove broke during the night shift, for example, while no one was working in administration to issue new PPE, the employee had to rely on their supervisor still having a supply. ‘It was difficult to fulfil our documentation obligations and keep track of consumption with the tally sheet,’ says Benjamin Döring, Head of Maintenance/Technology and Security Officer at ekka.Things are different today.
Things are different today. It is located right next to the old common room in the production area, where everyone walks past at the start of their shift. It is over 1.80 metres high and almost a metre wide. Inside, there is a circular shelf with space for up to 540 items. This is where the work gloves, route cards and much more are stored. Employees use the display to select what they need. Personalisation is used to determine who has access to which items. This prevents, for example, an employee from the ‘Chemistry’ department from receiving the gloves from the ‘Thermal’ department. This is made possible by an RFID chip. Incidentally, this is the same chip that ekka also uses for clocking in and out.
Good experience in use
And how was the innovation received in the company? ‘Our employees were very sceptical at first. However, acceptance is now very high. The employees are pleased that they can get the articles they need easily and at any time, and their line manager no longer has to manage the issue of articles personally,’ says Döring happily.
He has been working with Blumenbecker ‘forever’. He mainly knows the company as a supplier of tools. Sükrü Söyleriz, Blumenbecker sales representative at the Iserlohn site:
‘I presented Mr Döring with the various options available with automatic dispensers,’ says Söyleriz. After intensive discussions, the perfect vending machine model was finally found for ekka. The customer's verdict was correspondingly positive: ‘The cooperation with Blumenbecker is excellent. I don't need to say much more. Good advice, quick availability of the goods and also the handling of the vending machine project went smoothly,’ explains Döring.
‘Good advice, quick availability of the goods and also the handling of the vending machine project went smoothly.’
Benjamin Döring, Head of Maintenance/Engineering,
ekka Entlackung Ernst Kuper GmbH
The right product
Not all vending machines are the same. Every customer has different requirements. The devices are as different as the requirements. Sometimes only one flap opens, sometimes the entire door. ‘Precise load cell technology, cloud applications, fully automatic reordering of goods - almost anything is possible,’ says Axel Hildebrandt, Head of eProcurement at Blumenbecker. ‘Almost anything is possible’ with the i.cupboard 4.0 from DIGI SENS, for example. Blumenbecker presented the model at the maintenance trade fair in spring 2024 and it proved to be a magnet for visitors over the two days of the fair. The i.cupboard 4.0 is a storage system controlled by load cell technology, which, for example, has a person-specific allocation of goods removal, fully automatic reordering and inventory as well as a cloud app with reporting.
With personalised advice
It is important to find out which machine is the right one in discussions with the customer. Then it's down to the details. In the case of automatic connection, the customer's IT department must also be involved. ‘Good coordination is the be-all and end-all,’ says Hildebrandt, adding, ’with the right vending machine, our customer can reduce procurement and storage costs and increase productivity.’
Current issue as flip book
In this issue, you will find a wide range of customized solutions for our customers, whether in rail technology, industrial assembly or industrial services for passenger bridges in the shipping industry. Enjoy reading and discovering.
Flip book