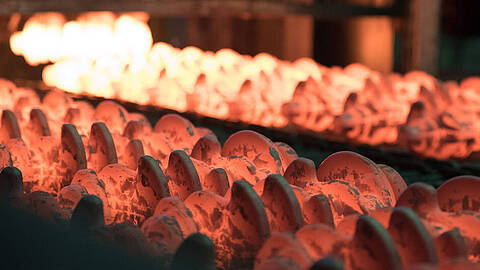
Automation of a quality testing machine
for crankshafts
Our client:
BHARAT FORGE CDP GmbH
BHARAT FORGE CDP GmbH is a leading supplier of forged chassis and engine components as well as non-automotive systems. The company develops, manufactures and supplies complex dropforged parts and performs machining and assembly work on truck and car chassis, powertrains, railway equipment and mechanical engineering components.
The commission
Several years ago Blumenbecker carried out automation work on a crankshaft quality testing machine at the BHARAT FORGE CDP works. The present contract required the entire installation to be fitted with state-of-the-art electrotechnical equipment, along with a matching mechanical upgrade. BHARAT FORGE CDP commissioned Blumenbecker Automatisierungstechnik GmbH to undertake the automation work on the new machine, modernise the existing line and replace the existing productionline robots with eight of the latest-generation KUKA KR QUANTEC robot systems.
Project scope
The project was planned and executed in accordance with BHARAT FORGE CDP‘s specifications and in close collaboration with the company. A very tight completion schedule was set for the automation of the new quality testing line. The contract was awarded in April 2015 and the handover to the client was completed in September of the same year. Other Blumenbecker companies were also integrated into the automation work in order to keep precise control over the complex production line at all times.
BHARAT FORGE CDP had introduced as much automation technology to the process as possible so as to ensure that the quality checks would be performed with maximum reliability and efficiency. Two robots load and unload the sandblasting unit with crankshafts, which are then taken on a belt conveyor to an eddy-current inductor for materials testing. A third robot then places the crankshafts in a flux testing machine that uses magnetic powder to identify any units exhibiting surface cracks, these being taken off-line on a separate belt. In the next stage of the operation a fourth robot sets the crankshafts on a turntable so that a visual inspection can be made. Appropriate routines are programmed into each of the tests in order to ensure that any units tested as defective are either automatically rejected or sent for re-working and repeat testing. The crankshafts then reach the last inspection station, where they undergo a final check before being packed into shipping containers.
The entire operation is extremely complex. For documentation purposes it is necessary to know at all times exactly where each part is along the test route, which stations it has gone through and what the next stage is. This information is logged to create a tracking system with full traceability for each batch of components.
The documentation previously created in EPLAN 5.70 was revised and redrafted in EPLAN P8. The mechanical layout of the switchgear was also made standard-compliant using the Pro Panel engineering tool. The existing routing function could then be used to generate the appropriate cable assemblies using Komax tools. The automation solution was implemented using the Siemens Tia Portal framework.
The existing quality testing line was modernised at the same time and the production line was also upgraded. This involved replacing the existing robots with eight new-generation KUKA KR QUANTEC robot units.
Our customer says:
»Quality is the key objective.«
Technical data in brief
Quality test line |
Production line |
---|---|
safety control system: Simatic 1516F-3 PN/DP |
safety control system: Simatic 317F-2 PN/DP |
interlink to field devices: PROFINET |
interlink to field devices: PROFINET |
high-level network: PROFINET |
high-level network: PROFINET |
communication partners: 32 |
robots: eight [KR QUANTEC] |
robots: four [KR QUANTEC] |
programming environment: Simatic Manager |
programming environment: Simatic S7 TIA Portal |
special software specifications: restructuring of the existing |
special software specifications: |
throughput: 250 units per hour |